How Does Die Cutting Pricing Work?
Ordering die cut parts can feel like asking a server to appraise a dish that’s not on the menu: how do you assign a price tag to a meal you’ve never seen before?
Because every die cut order has a unique design, your die cut cost depends on the anticipated tooling, material, and labor cost.
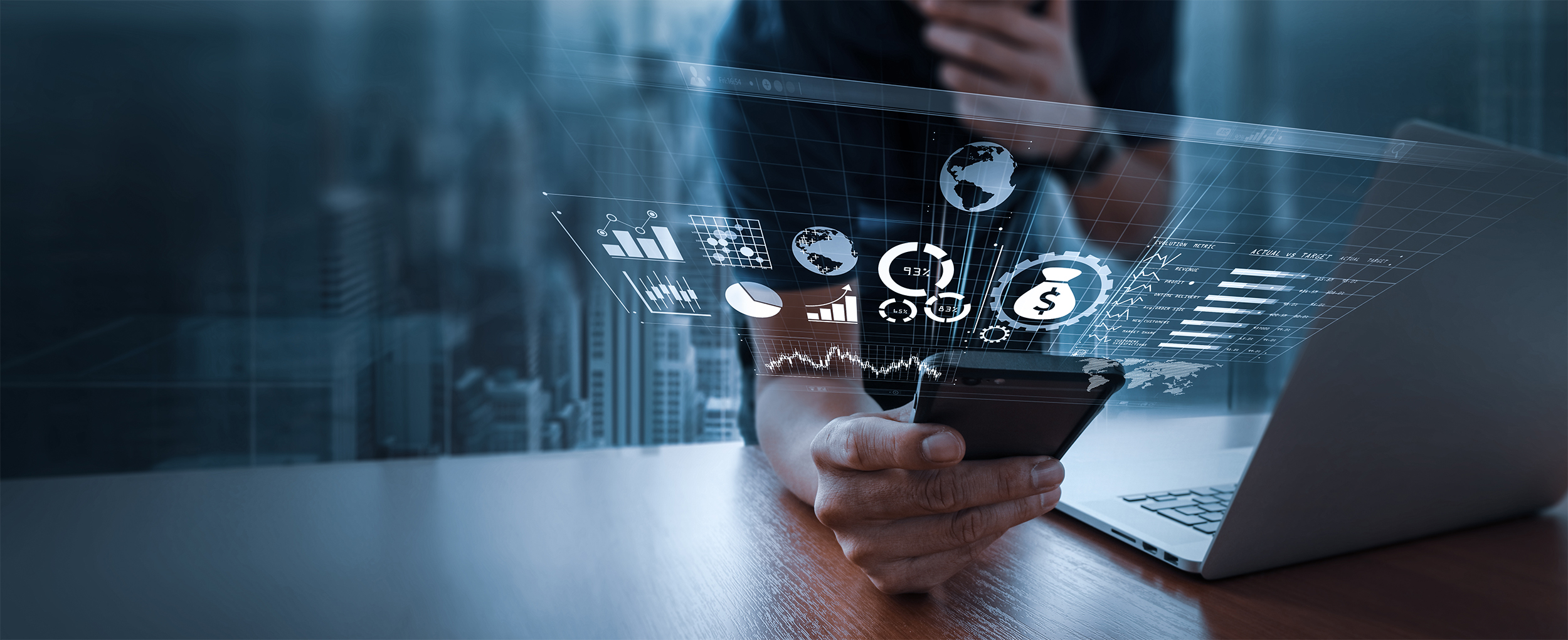
Tooling
If you’ve selected laser die cutting, congratulations! You’re safe from the cost of tooling. However, the other die cutting methods will require you to purchase a custom tool in the shape of your desired product.
Your die cut tooling cost will vary based on the complexity of your design. Die cut parts with simple designs are cheaper than complex parts because the complexity of a design correlates with the cost of tooling. Designs with multiple layers or materials, tighter die cut tolerances, and other complex part geometries are more challenging and lead to more expensive tooling.
Lastly, remember that die cut tools will inevitably need re-tooling if you plan a long-term project or use abrasive materials. Like any other blades, dies must be sharpened or replaced once they’ve worn out, but the exact time limit depends on your material.
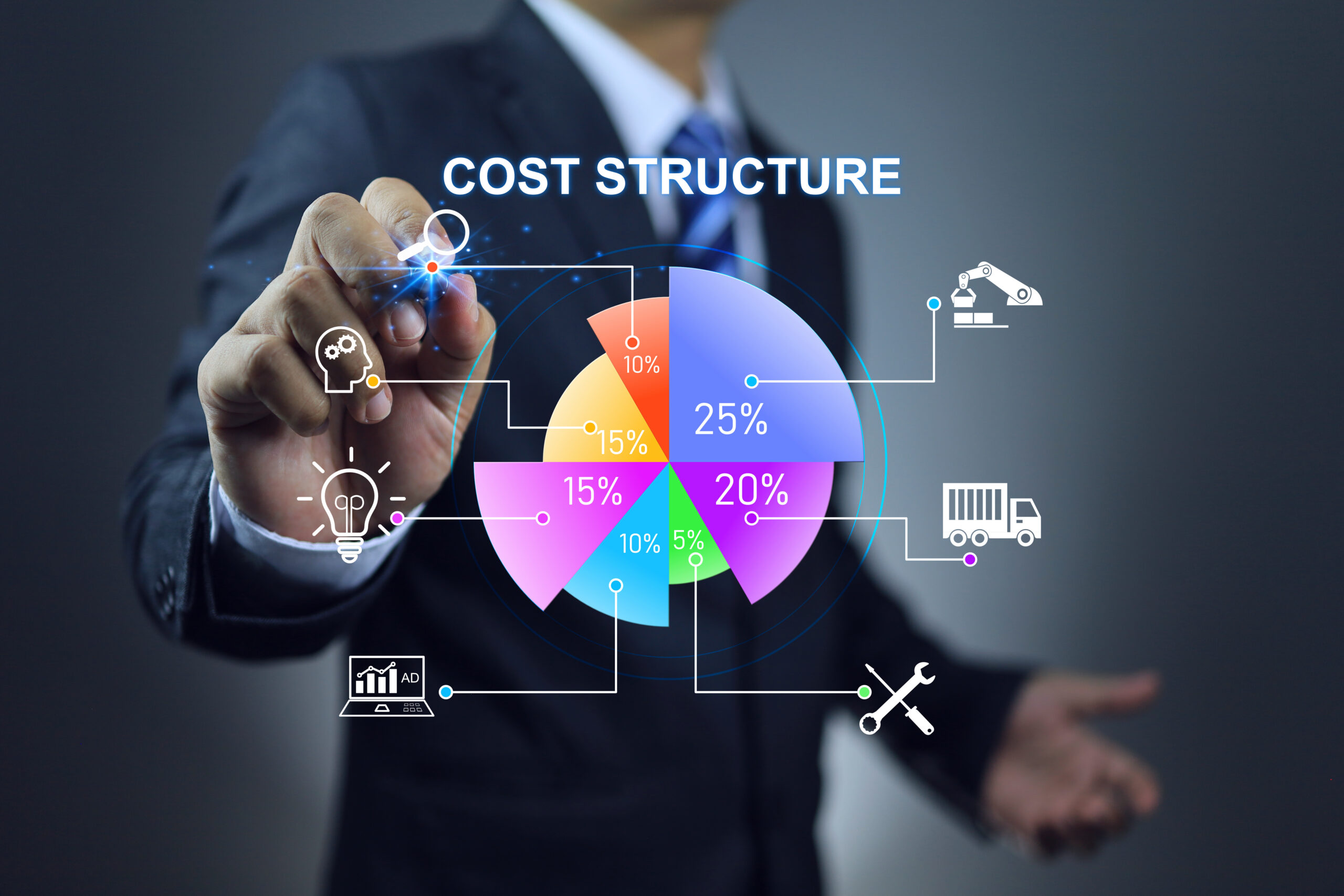
Material
The material you select plays a significant role in the tooling of your part and whether it can meet the correct tolerances. Material costs make up about 75-80% of your total die cutting expenses, which can have a diverse affect upon smaller organizations.
Most converters will start off by using rolls of pre-made, standard length material and to offset the cost, they sell material in a Minimum Order Quantity (MOQ). The minimum order quantity determines the amount of product customers have to buy. In most cases a converter will tell you that your material is only sold in roll form and so the minimal material you can purchase is full roll. This can have a high impact on the cost, but tends to save most organizations money in the long run.
Converters may also take into account the material waste when determining the material cost. By working with an experienced engineer you can decrease the waste of your production run by having parts spaced to maximize the surface area of the material.
Using materials that needs a particular type of blade or additional processing can also increase the final cost of the material.
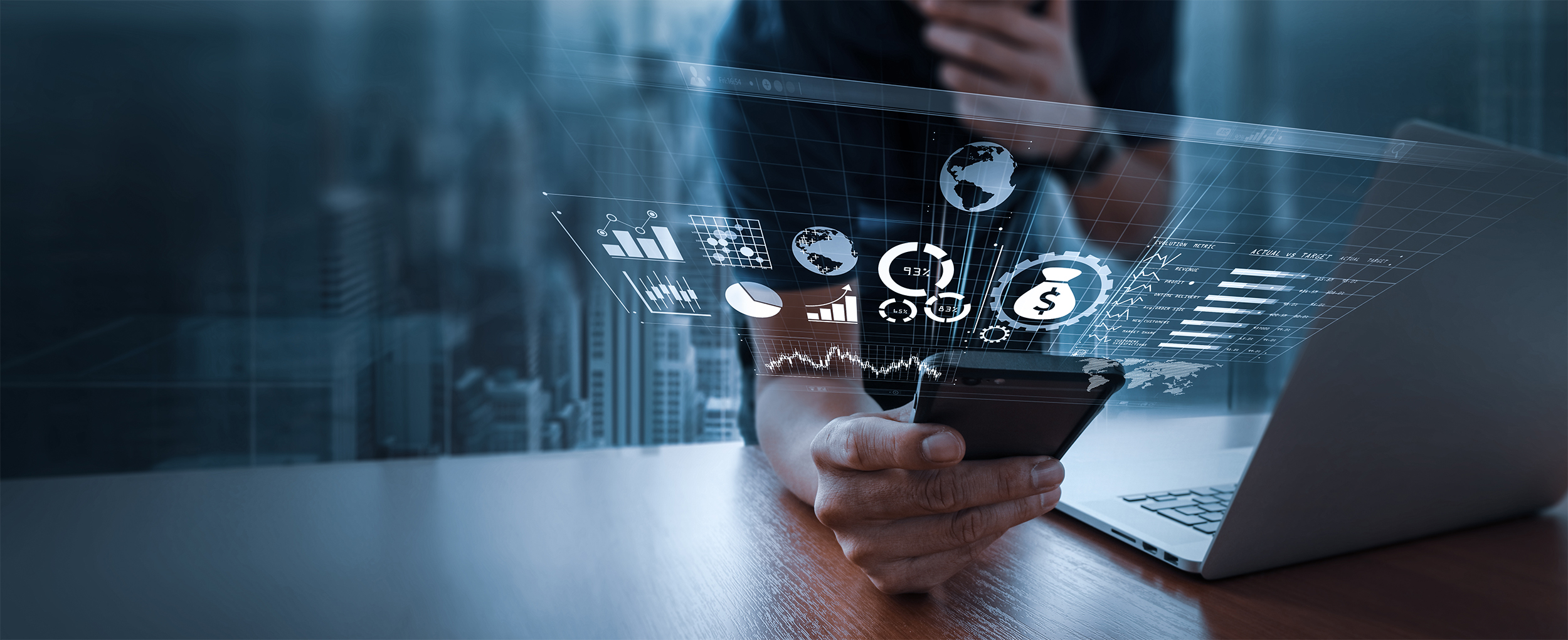
Labor Cost
The labor cost of die cutting plays a significant role in the overall production expenses, making it an essential consideration for businesses engaged in manufacturing processes. These labor cost includes machine set-up, testing, production run time, and breakdown.
Die cutting requires a skilled worker to operate specialized machinery and handle intricate dies.These highly trained professionals carefully position the material on the machine’s bed and ensure accurate alignment before activating the press mechanism. Their expertise is vital in minimizing errors and maximizing efficiency throughout the die-cutting process.
As each project may involve different designs and sizes for die cuts, operators mustpossess versatility to adapt their techniques accordingly. Moreover, depending on complexity levels and intricacy of patterns involved in a particular job order—whether it be simple outlines or intricate design—they may need to adjust settings on the machine accordingly. This meticulous attention to detail ensures clean cuts without any unwanted fraying or tearing during production.
Furthermore, labor costs associated with die cutting extends beyond mere operational tasks. Skilled workers are responsible for maintaining equipment cleanliness and performing routine maintenance checks to keep machines running smoothly—a key factor contributing to productivity levels within an organization. Understanding how labor costs are impacted by various aspects like skill level requirements and maintenance duties enable manufacturers to assess budgetary considerations accurately when planning their projects involving die cutting operations.