Why Choose Die Cut Parts
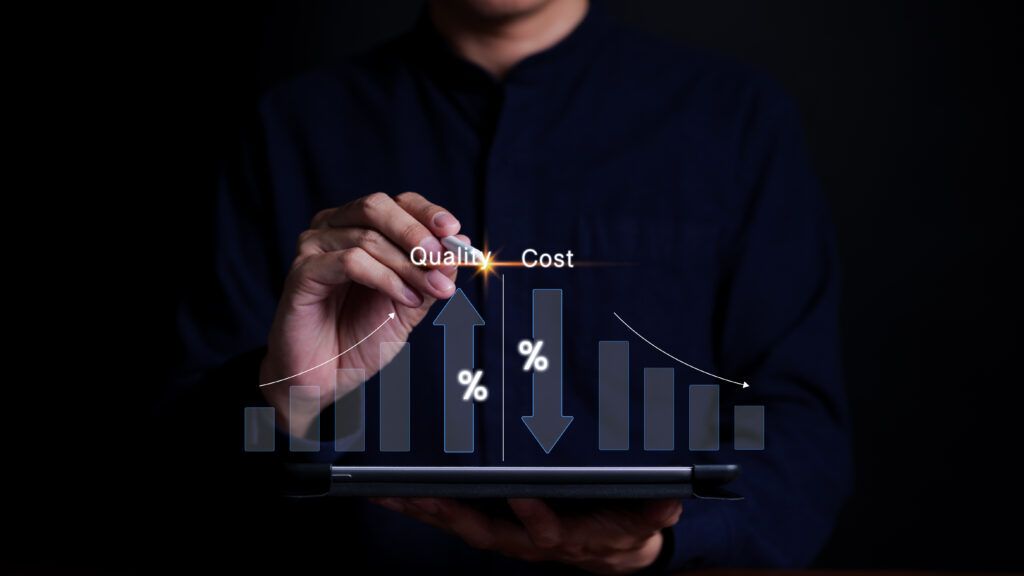
Using die cut parts and the die cutting process needs to be thought out and well designed by a converting specialist for it to be a cost effective solution for your business. Essentially, if you are looking for a series of custom, identical components, die cutting promise to improve production and final product quality. Consistent parts lead to better applications and fewer mistakes, saving time and money, while assisting with the ease of someday automating your production or scaling up your business.
Although rolls of tape cost less than die cut adhesives, they can take longer to apply, require more labor, and create a larger amount of material waste. Rolls of tape also lack the accuracy of die cut adhesives. Operators are also left on their own to figure out the best method of application, which can cause inconsistencies and errors.
Not to mention the need to hire additional staff for these task. Even with the budget to hire more people, die cutting machines can produce adhesives faster and more accurately than any employee with a pair of scissors. Often, it requires more direct contact with the final product, which can lead to issues in almost every industry.
Using a die cut solution will allow you to consolidate multi-process projects and avoid unnecessary shipping costs. Adapting designs to a die cut press increases production speed and part accuracy.
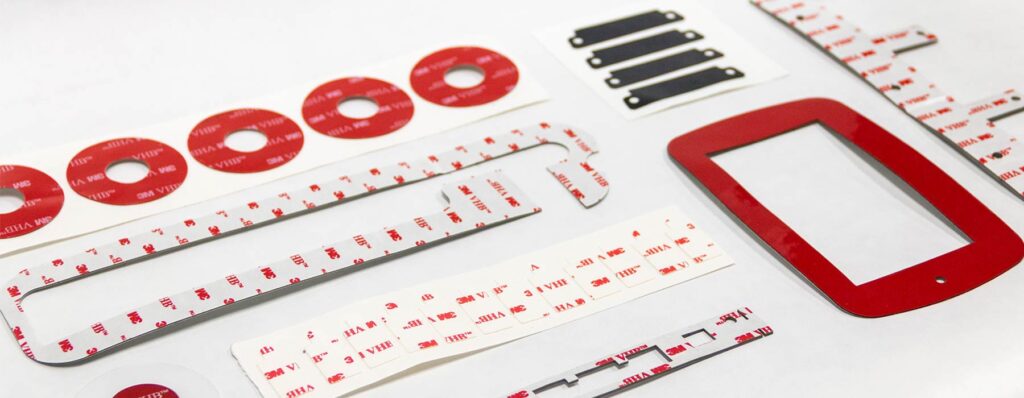