How Die Cut Adhesive Materials Can Improve Your Assembly Line Efficiency
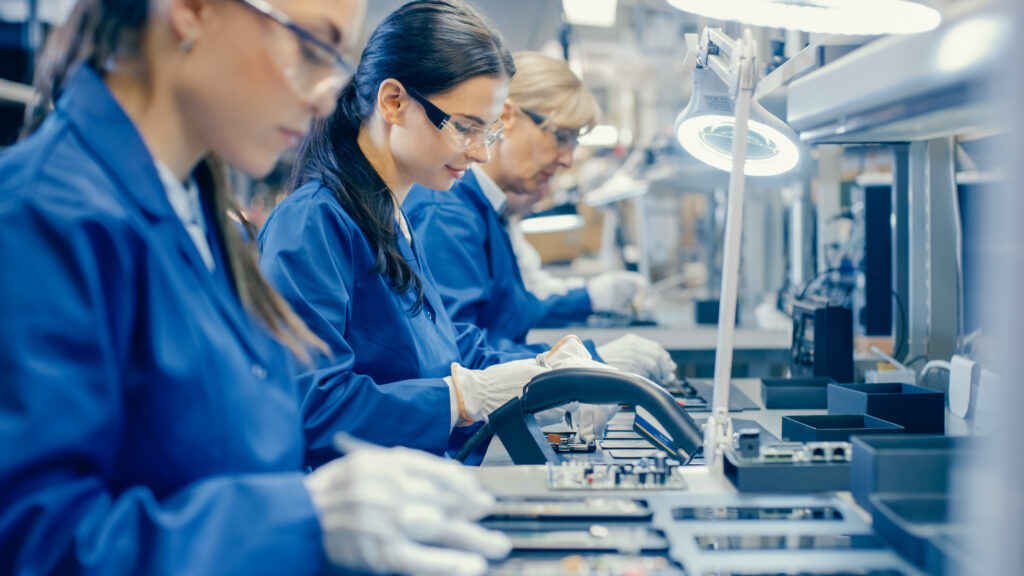
As the demand for faster and more efficient production increases, you need to make sure that your assembly line is up to the task. One of the most reliable and cost-effective ways of doing this is by investing in die-cut adhesive materials. In this blog article, we will be taking a look at how these materials can improve your assembly line efficiency and provide you with a better overall result.
Introduction to Die-Cut Adhesive Materials
Die-cut adhesive materials are versatile and essential tools in many industrial and commercial applications. From gaskets and seals to packaging and product assembly, die-cut adhesives can be found in a variety of industries.
Die-cut adhesive materials are made by cutting adhesive-coated material into a desired shape using a die. This process allows for precise shapes and sizes to be cut, which is essential for many applications.
Die-cut adhesives offer many benefits over other types of adhesive materials. They are easy to apply, have a long shelf life, and provide a strong bond. Additionally, die-cut adhesives can be custom-made to fit your specific needs.
If you are looking for an efficient way to improve your assembly line efficiency, consider using die-cut adhesive materials.
Benefits of Using Die-Cut Adhesive Materials
Die-cut adhesive materials are a type of self-adhesive material that is die-cut to a specific shape and size. Die-cut adhesive materials are used in a variety of industries, including the automotive, electronics, and medical industries.
Die-cut adhesive materials offer a number of benefits over traditional adhesive materials. Die cut adhesive materials are more precise, meaning that they can be applied more accurately to a surface. This results in less waste and fewer defects.
Die-cut adhesive materials are also easier to apply than traditional adhesive materials. This is because the die-cutting process creates a consistent thickness and application pressure, which makes it easier to apply the material evenly. This results in faster assembly times and fewer defects.
Types of Die Cut Adhesive Materials
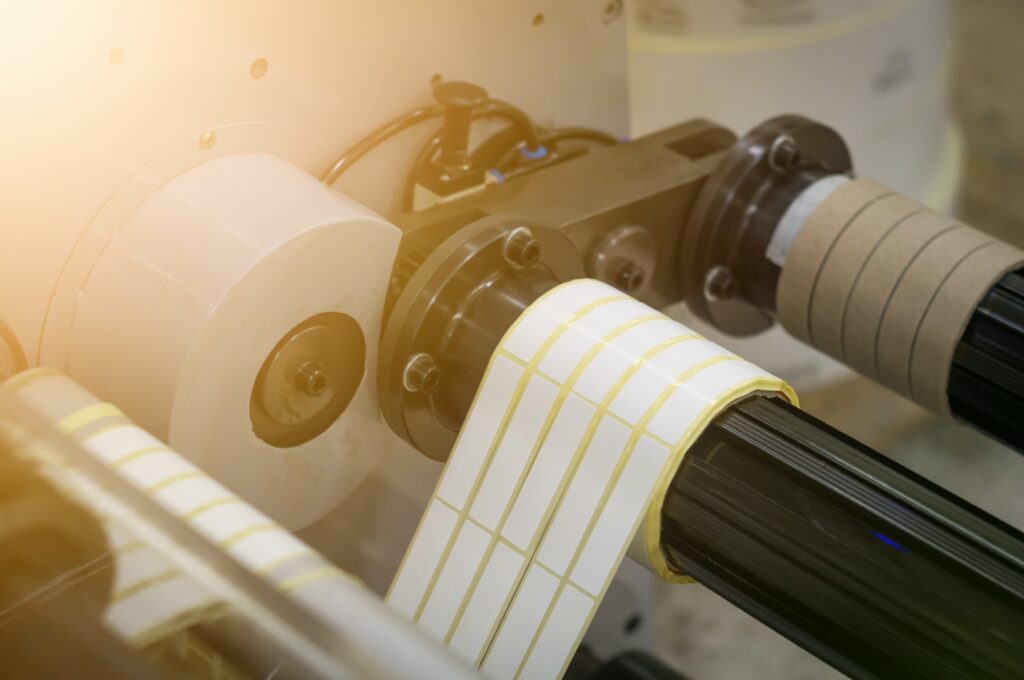
Adhesive materials are available in a variety of die-cut shapes and sizes to fit your specific assembly needs. Here is a closer look at the three most common types of die-cut adhesive tape materials:
1. Pressure-sensitive adhesive tapes: Pressure-sensitive adhesive tapes are ideal for light-duty applications requiring quick bonding and easy handling. They can be applied manually or with automated equipment, and cure quickly at room temperature. They are commonly used in applications where high bonding strength is required, such as in automotive and aerospace assembly. PSAs are available in both water-based and solvent-based formulations.
2. Hot melt adhesive tapes: Tapes with hot melt adhesives offer high bond strength and fast bonding speed for demanding applications. The adhesive is applied using hot melt adhesive guns and cures at room temperature. They offer high bonding strength and quick setting times, making them ideal for use in high-speed assembly applications. HMAs are available in both solid and liquid formulations.
3. Epoxy adhesive tape: Epoxy adhesive tapes provide superior bond strength and durability for heavy-duty applications. The adhesive requires mixing before application, and cure at room temperature after being exposed to air or ultraviolet light. Their excellent bonding strength makes them well-suited for use in demanding industrial applications.
4. Acrylic adhesive tapes: Acrylic adhesives bond quickly and have good resistance to heat, cold, and UV light exposure. They typically have shorter shelf lives than other adhesive types due to their sensitivity to moisture vapor.
Choosing the Right Die-Cut Tape Material for Your Assembly Line
If you’re looking to improve the efficiency of your assembly line, die-cut adhesive materials can be a great way to do so. But with so many different materials and applications available, how do you choose the right one for your needs?
Here are a few things to consider when choosing die-cut adhesive materials for your assembly line:
1. What type of surface will the material be applied to?
2. How much weight will the material need to support?
3. What temperature range will the adhesive material be exposed to?
4. What chemical resistance does the adhesive material need to have?
5. How long does the adhesive need to last?
Once you’ve considered these factors, you can narrow down your choices and select the die cut adhesive material that’s best suited for your assembly line needs.
Common Applications of Die Cut Adhesive Materials in Assembly Lines
Die cut adhesive materials are commonly used in assembly lines to improve efficiency. By eliminating the need for manual labor, die cutters can help reduce the time it takes to complete a task. In some cases, they can also improve the quality of the final product.
One of the most common applications of die cut adhesive materials is in the automotive industry. Die cutters are often used to create parts for car doors and other components. They can also be used to create labels and decals for cars.
Another common application of die cut adhesive materials is in the electronics industry. Die cutters are often used to create parts for circuit boards and other electronic components. They can also be used to create labels and decals for electronics products.
Die cut adhesive materials can also be used in the food industry. Die cutters are often used to create parts for food packaging and other food-related products. They can also be used to create labels and decals for food products.
Tips and Tricks on How to Use Die Cut Adhesive Materials Effectively
When it comes to die cut adhesive materials, there are a few tips and tricks that can help you get the most out of them. Here are a few to keep in mind:
1. Make sure the surface you’re applying the adhesive to is clean and dry. Any dirt or moisture will affect the adhesive’s bond.
2. Apply pressure evenly when affixing the adhesive. This will help ensure a strong bond.
3. Use a sharp cutter when trimming the adhesive to size. This will give you clean, straight cuts and help avoid any fraying or peeling.
4. If you need to remove the adhesive, do so slowly and carefully to avoid damaging the surface beneath.
Conclusion
In conclusion, die cut adhesive materials are a great way to improve the assembly efficiency of your line without sacrificing quality. With its cost-efficiencies, convenience and flexibility, these materials offer an excellent solution for any business looking to optimize their production processes. Whether you choose foam tapes or pressure sensitive adhesives, you can be sure that your products will meet all expectations in terms of accuracy and reliability.